N/A
Construction
NMW/NMWR/PRMW-pumps are single stage volute casing pumps with closed impellers, back-pull-out design, with end suction and top centerline discharge flange. Foot mounted casings are provided as standard. Centerline mounted design is available as an option. Performance data and flange-to-flange dimensions comply with EN 22858 (ISO 2858).
Magnetic coupling
The single elements of the multipolar magnetic coupling are manufactured of a permanent magnet material "Cobalt-Samarium Rare Earth" with unlimited lifetime. The magnets in the internal rotor are completely encapsulated; no contact with liquid occurs.
Energy is transmitted to the hermetically sealed liquid end by the outer drive magnets, passing motive force through the containment shell to the internal drive magnets. Inner and outer magnets are locked together by the magnetic field lines and are working synchronously without any slip.
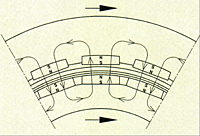
The inner magnet ring transmits the required torque directly to the impeller. Overload of the magnetic coupling and slipping will not effect demagnetization if a reliable monitoring device prevents overheating of the magnets. During operation, the rotating field lines pass through the metallic containment shell and generate magnetic losses. The magnetic couplings are sized for direct- on-line starting of the electric motors. The transmissible power of a coupling depends on the axial magnet length. The couplings are sized for the maximum power consumption of the rated impeller at the end of performance curve. The rated coupling power can be increased by mounting an additional series of magnets, required e.g. when installing a larger impeller and respectively, motor.
Internal clearances
The internal clearance between inner magnets and containment shell depends on the wall thickness of the containment shell. However, a minimum clearance of 1 to 2 mm (0.039 - 0.078") is provided in any case. This, together with wear resistant sleeve bearings, allows handling of fluid with solids.
Monitoring
Temperature monitoring, power monitoring, dry running protection devices, leakage detection systems are available. Ask DICKOW engineers for further details.
NPSH-Conditions, Inducer
To avoid cavitation, the impellers of the NMW/NMWR/PRMW-pumps are designed to achieve low NPSH-values. For pumps with discharge above 50 mm (2"), optional inducers are available for further improvement of NPSH-required conditions. The inducers are designed such that NPSH- improvement is given from minimum flow up to BEP.
Retrofit of inducers on site is possible by remachining the volute casing, without changing the suction pipe.
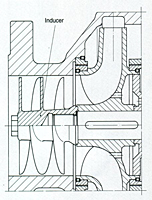
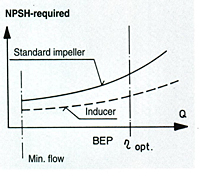
Drain Connections
Volute casing and magnet end have separate drain connections.
Venting System
During start-up and filling of the system with open suction valve, the pumped liquid enters the magnet end through holes in the sleeve bearings and the gap between pump shaft and bearing housing. Remaining air in the containment shell will be vented by the two valve venting system according to the manual instructions.
Balanced thrust loads
The thrust loads of the closed impellers are balanced by wear rings, balance holes in the impeller hub, and back vanes. Residual forces on the impeller are acting in the suction flange direction. These forces will be balanced by the rotor design. The difference between the constant pressure at the rear rotor area and the variable pressure at the front side creates a counter force acting in direction to the containment shell. The value of this reaction force depends on the variable gap S. This meansthat the internal rotor floats until the forces at impeller and rotor are balanced. The thrust bearings work as start-up rings only.
|